Keeping farm machinery clean is crucial for its optimal performance and long lifespan. When muck, dirt, and debris accumulate on equipment surfaces, it can pose risks to both functionality and structural integrity.
Preventing rust formation: Cleanliness plays a key role in preventing rust, which can develop when moisture and muck combine on machinery surfaces. Rust not only damages the appearance of machinery but also weakens metal components, leading to expensive repairs and safety concerns.
Finding problems sooner: Clean machinery makes it easier to spot potential issues before they become major problems. Regular inspection and cleaning allow farmers to identify signs of wear, damage, or malfunction promptly. This proactive approach minimises downtime and ensures smooth farm operations.
Simplifying part replacement: Clean machinery simplifies the process of replacing worn-out or damaged parts. With no muck or dirt to contend with, accessing critical components is easier and less time-consuming. Clean surfaces also promote better adhesion of lubricants and protective coatings, enhancing machinery durability and performance.
Steps to Properly Clean Farm Machinery
Cleaning farm machinery effectively requires a systematic approach to remove dirt, muck, and grime accumulated during agricultural operations. Here are the essential steps to ensure thorough cleaning and maintenance of your equipment:
- Pre-cleaning Inspection: Begin by conducting a thorough inspection of the machinery to identify areas with heavy buildup. Pay attention to hard-to-reach areas such as joints, crevices, and underneath the equipment.
- Removing Large Clumps: Use tools like wooden poles or scrapers to remove large clumps of dirt and debris from the machinery surfaces. This initial step helps to loosen stubborn accumulations and prepare the equipment for deeper cleaning.
- Wetting the Surface Muck: Before power washing, wet the surface muck with water or a mild cleaning solution. Wetting the muck helps to soften it, making it easier to remove during the cleaning process.
- Using Proper Cleaning Techniques: Employ effective cleaning techniques such as pressure washing, scrubbing, and using handheld brushes to dislodge stubborn dirt and debris. Focus on removing accumulated muck from critical components, including engine compartments, hydraulic systems, and undercarriages.
- Drying: After cleaning, ensure the machinery is thoroughly dried to prevent moisture-related issues and rust formation. This can be as simple as letting the machine air dry under a roof, for more intricate areas, absorbent towels or air blowers can remove excess water from surfaces and components.
Keeping Steel Wearing Parts Rust Free
Ensuring metal parts working in the soil are kept rust-free is essential so that the implement works properly. Take the example of a plough mouldboard. When a plough is not cleaned and the mouldboards greased after use, they will be rusty when it is next used.

The rusty mouldboard will hold onto the soil which stops the furrows from turning over properly, this will give the tractor driver a lot of extra work getting out and using a spade to clean the boards ever so often until they shine up.
The following points are why you should keep a ploughs mouldboards clean and shiny.
- Efficient Soil Turning: A smooth metal plough mouldboard allows for seamless and efficient soil turning, letting the plough cut through the soil with minimal resistance. Conversely, a rusty or rough surface can cause friction and drag, hampering the plough’s ability to penetrate the soil effectively.
- Reduced Soil Compaction: A smooth mouldboard minimises soil compaction by creating clean, well-defined furrows. Well-turned soil promotes healthier root growth and water absorption, leading to improved crop health and better yields. Conversely, a rusty mouldboard might result in uneven furrows and compacted soil, hindering crop development and yield potential.
- Improved Seedbed Preparation: A smooth metal plough mouldboard ensures an optimal seedbed for planting by evenly spreading soil and organic matter across the field. This encourages uniform seed germination and emergence, resulting in consistent crop growth and maturity. A rusty or uneven mouldboard may leave soil clumps and debris in the furrow, compromising seed-to-soil contact and seedling establishment.
- Minimised Soil Disturbance: Smooth plough mouldboards minimise soil disturbance during ploughing, preserving soil structure and organic matter content. This helps mitigate erosion risks and conserve essential nutrients for plant growth. In contrast, rusty or uneven mouldboards may disrupt soil excessively, leading to erosion and nutrient loss over time.
- Enhanced Fuel Efficiency: Smooth metal plough mouldboards improve fuel efficiency by reducing the power needed for ploughing operations. With less resistance and drag, tractors can operate more efficiently, using less fuel per hectare ploughed. This results in cost savings for farmers and a reduced environmental impact.
Oiling Farm Machinery Before Storage
Applying oil to machinery using either a paintbrush or a compressor and oil applicator is a common practice in farm maintenance. It helps to lubricate moving parts, prevent rust, and extend the lifespan of equipment. Here’s how it’s done:
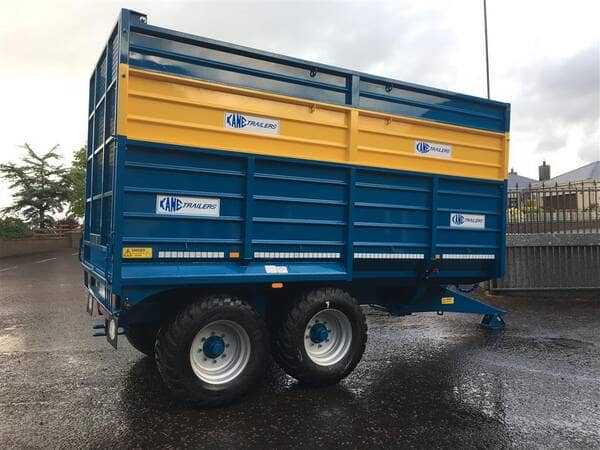
- Preparation: Before applying oil, ensure that the machinery is clean and dry. Remove any dirt, debris, or moisture that may be present on the surface. This ensures that the oil can be applied evenly and effectively.
- Selecting Clean Oil: It’s essential to use clean oil for lubrication. Burnt or contaminated oil can have adverse effects on both machinery and health. Ensure that the oil being used is clean and free from impurities.
- Applying Oil Safely: The safest way to apply oil to machinery is by using a brush and a pot to hold the oil. If you have lots to do a compressor and oil applicator is quicker. To avoid overly fine mist particles, it’s recommended to set the compressor to lower pressure settings – this increases the droplet size of the oil which is less dangerous to work with. When applying oil, it’s important to wear appropriate personal protective equipment, including a mask to prevent inhalation of oil mist. This protects your respiratory system from exposure to airborne particles and fumes. Ensure the task is carried out in an open space – not inside a shed.
- Using a Compressor and Oil Applicator: A compressor and oil applicator are handy tools for applying oil to machinery. The compressor generates compressed air, which is then used to atomise the oil, creating a mist that can be sprayed onto the machinery surfaces.
- Spraying Machinery Surfaces: Spray the clean oil onto the machinery surfaces using the oil applicator. Pay particular attention to moving parts and areas prone to rusting.
- Proper Drying: Allow the excess oil to drip dry after the application before storing the machinery. This helps prevent oil dripping on the shed floors.
- Avoiding Plough Mouldboards: While oil can be applied to trailers and other machinery, plough mouldboards should be greased instead of oiled. Grease provides a thicker cover and lasts longer on metal surfaces than oil, which can wear off in a month or two.
Final Thoughts..
Cleaning and maintaining farm machinery is vital for performance, longevity and safety. Thoroughly cleaning machinery makes it easier to maintain and see problems arising. If machines are to be stored for extended periods of time they can be further protected by applying a film of clean oil or grease to steel wearing parts.