Harvesting oats involves combining specific techniques and adjustments to achieve the best possible yield and quality. Oats, a widely consumed cereal grain valued for its adaptability and nutritional content, require careful attention to detail during harvesting. In this guide, we will examine the essential strategies for successful oat harvesting. From timing and equipment selection to weather conditions and post-harvest handling, each aspect contributes significantly to achieving optimal efficiency and profitability.
Combining Techniques for Harvesting Oats: Maximising Yield and Quality
Oats, a versatile and nutritious cereal grain, require careful harvesting techniques to ensure optimal yield and quality. Combining various harvesting methods tailored to oat cultivation can significantly enhance efficiency, minimise losses, and preserve the integrity of the harvested grain. Here’s a comprehensive exploration of techniques for harvesting oats:
Timing Optimisation: Harvesting oats at the right stage of maturity is crucial for achieving maximum yield and quality. Typically, oats are harvested when the kernels reach maturity but still retain some moisture. Monitoring the crop’s development and assessing moisture content are essential for determining the optimal harvest time. Harvesting too early can result in underdeveloped kernels, while delaying harvest may lead to shattering and grain losses.
Equipment Selection: Choosing the appropriate harvesting equipment is paramount for efficient oat harvesting. Selecting a combine harvester which can fine-tune the threshing ensures optimal performance. Look for combines with fully adjustable settings for threshing, separating, and cleaning to accommodate varying oat conditions. Headers with flexible reel configurations and cutting platforms enhance the gathering process, reducing grain losses and minimising crop damage.
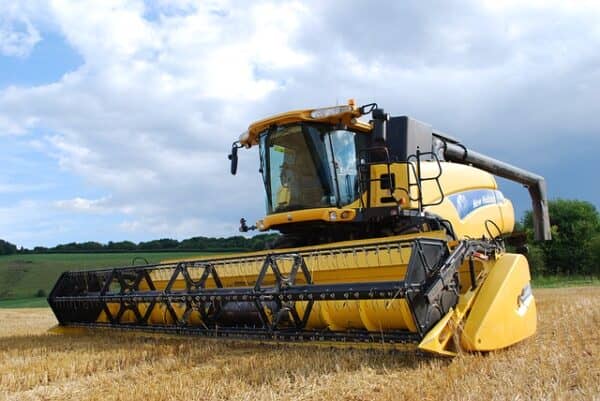
Weather Considerations: Weather conditions play a significant role in oat harvesting. Ideally, aim to harvest oats during dry weather to minimise grain moisture content and prevent potential spoilage. Harvesting in wet conditions can lead to grain quality issues and complicate subsequent drying and storage processes. Monitoring weather forecasts and adjusting harvesting schedules accordingly can help mitigate risks associated with adverse weather conditions.
Optimising Harvesting Techniques: Fine-tuning harvesting techniques is essential for maximising efficiency and preserving grain quality during oat harvest. Set combine parameters such as cylinder speed, concave clearance, and fan speed to optimise threshing and cleaning operations while minimising kernel damage and impurities. Adjusting ground speed based on crop conditions and equipment capabilities ensures thorough harvesting without sacrificing quality.
Labour Management: Efficient allocation of labour resources is critical for timely and effective oat harvesting. Coordinate harvesting schedules to coincide with peak crop maturity and labour availability. Adequate manpower ensures smooth harvesting operations and minimises delays, allowing for optimal use of equipment and resources.
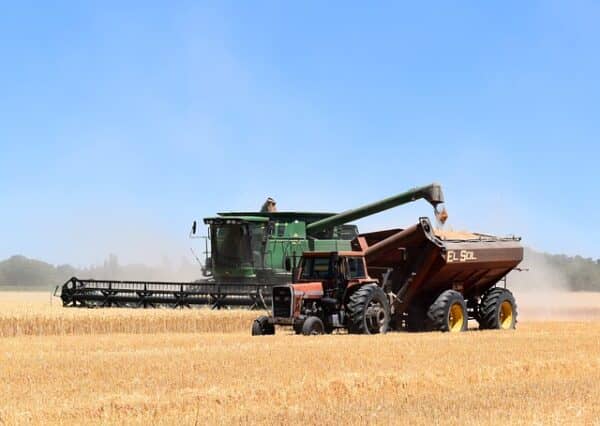
Post-Harvest Handling: Proper post-harvest handling practices are essential for preserving the quality and marketability of harvested oats. Thoroughly clean and inspect harvesting equipment after each use to remove debris and prevent contamination. Implement effective storage solutions to protect harvested grain from moisture, pests, and spoilage, ensuring long-term viability and market value.
Quality Control Measures: Implement stringent quality control measures throughout the harvesting process to maintain grain integrity and meet market standards. Regularly monitor harvested oats for impurities, damage, and moisture content. Utilise advanced technologies such as moisture meters and grain analysers to assess grain quality and make informed decisions regarding storage and marketing.
Combining Adjustments for Harvesting Oats:
Harvesting oats effectively involves making specific adjustments that suit the crop’s unique requirements. Oats are known for their nutritional value and adaptability, demanding careful handling to maintain quality and yield.
Fine-tuning Combine Settings: Adjust the combine’s settings for efficient oat harvesting. Oats prefer a more gentle threshing setting to prevent excessive kernel damage. Configure the cylinder speed and concave clearance specifically for oats to achieve optimal threshing without overprocessing.
Header Height Adjustment: Adjust the header height to ensure efficient gathering of oat plants while minimising grain losses and shattering. Keeping the header close to the ground facilitates the collection of low-growing oats, preventing valuable grain from being left behind.
Reel Speed Optimisation: Optimise the reel speed to effectively feed oat plants into the combine without causing unnecessary plant damage or wrapping. A slower reel speed may be beneficial for oats, especially in uneven or lodged crop conditions, allowing for better control during harvesting.
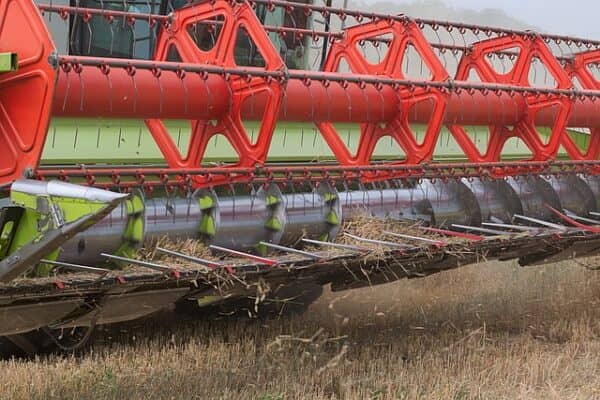
Weather-Responsive Harvesting: Remain adaptable to weather conditions during oat harvesting. Preferably, conduct harvesting operations during dry weather to prevent grain spoilage and maintain quality. However, if harvesting in damp conditions is unavoidable, consider making adjustments to minimize grain moisture intake and subsequent drying requirements.
Stubble Management: Adjust the cutting height to leave an appropriate stubble length after harvesting oats. Maintaining adequate stubble height supports soil conservation efforts by reducing soil erosion and enhancing soil structure. Moreover, the stubble can serve as valuable organic matter when incorporated into the soil through subsequent tillage practices.
Continuous Quality Control: Implement comprehensive quality control procedures throughout the harvesting process. Regularly inspect the harvested oats for any signs of impurities, including weed seeds, debris, or damaged grains. Utilize onboard monitoring systems to promptly identify and address any mechanical issues affecting harvesting efficiency or grain quality.
Thorough Cleaning and Maintenance: Perform regular cleaning and maintenance tasks on harvesting equipment to ensure optimal performance and longevity. Clear out any debris or buildup that may impede the harvesting process and inspect critical components for signs of wear or damage. Addressing maintenance needs promptly helps minimize downtime during peak harvesting periods.