The combine harvester represents a significant advancement in agricultural technology, merging cutting, threshing, and winnowing into one continuous operation. This guide delves deeper into its intricate mechanisms and historical progression.
1. Historical Overview
- 1830s Beginnings: Hiram Moore’s invention, the horse-drawn combine, initiated a new era in grain harvesting, drastically reducing manual labour.
- Late 19th Century – Steam Power: Steam-powered combines, with their increased power and capacity, allowed for the harvesting of vast fields, setting the stage for industrial-scale agriculture.
- Early 20th Century – Internal Combustion Engines: This era saw combines becoming more compact and efficient, adapting to various crop types, facilitated by the advent of the internal combustion engine.
- Post-World War II Advancements: Post-war, technological advancements accelerated, leading to combines with improved performance, reliability, and adaptability to different crops and terrains.
2. Main Components and Their Functions
- Cutting Head: Engineered for precision, it is adjustable to varying crop heights and conditions, ensuring an efficient and clean cut.
- Reel: Its design and speed are key for efficiently guiding the cut crops into the threshing mechanism without clogging or loss.
- Threshing Drum: This is where the bulk of the work happens. Its speed and force are critical for effectively separating grains from stalks.
- Concave: Its proximity to the threshing drum is adjustable to cater to different grain sizes, ensuring effective separation without damage.
- Straw Walkers: These components play a crucial role in separating the last bits of grain from the chaff, a process that requires fine-tuned mechanical synchronization.
- Cleaning System: This system, using a combination of airflow and sieves, must be precise to ensure that the grain is clean and free of impurities.
- Grain Tank: Its capacity is vital for operational efficiency, determining how long the combine can operate before needing to unload.
- Unloading Auger: The design of the auger is critical for quick and efficient transfer of grain, a key factor in operational time management.
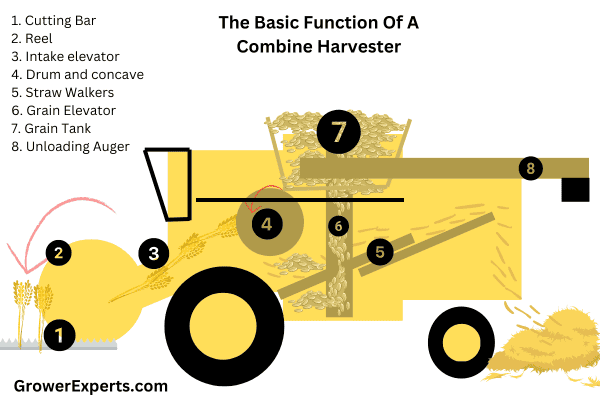
3. Operational Stages Explained
- Stage 1: Cutting. This stage sets the tone for the efficiency of the entire operation, requiring sharp, well-maintained blades for optimal performance.
- Stage 2: Feeding. The reel’s speed and angle are critical for a smooth flow into the threshing drum, a factor that can significantly affect overall efficiency.
- Stage 3: Threshing. The power and design of the threshing drum are central to its ability to separate the grain from the stalk without waste or damage.
- Stage 4: Separating. This stage requires a delicate balance, efficiently separating grain from chaff without loss.
- Stage 5: Cleaning. The effectiveness of the cleaning system impacts the quality of the final product, making it a critical stage in the process.
- Stage 6: Storing and Unloading. This final stage is about managing the harvested crop, where the capacity and efficiency of the grain tank and auger are paramount.
4. Technological Advances
- GPS and Automation: These technologies have transformed the combine into a highly efficient, nearly autonomous machine, reducing manual input and increasing precision.
- Variable Rate Technology: VRT adjusts the machine’s settings in real-time, responding to variations in crop density and soil conditions, maximizing yield and resource efficiency.
- Yield Monitoring Systems: These systems provide valuable data, enabling farmers to make informed
The combine harvester, from its inception to its current state-of-the-art form, showcases the remarkable journey of agricultural technology. It stands as a testament to human ingenuity in optimizing food production, highlighting the balance between efficiency and sustainability in modern agriculture.